Fabrication Methods
Recommended General Fabrication Practices
- General safety precautions associated with use of manual and powered tools and equipment must be observed.
- During sanding, machining or sawing operations a long sleeved shop coat or coverall and dust mask must be worn. The dust created presents no serious health concerns and is non-toxic, but can cause skin irritation. Protective barrier creams can be used to reduce or eliminate the amount of irritation.
- When drilling, routing or sawing avoid applying excessive pressure and this will tend to dull the tool.
- During any machining operation avoid generating excessive heat as this will soften or burn the bonding resin resulting in a ragged rather than a clean-cut edge.
- Proper support of the pultruded material during cutting will prevent warping and chipping at the cut edges.
- Seal all holes and cut edges with an acrylic spray or epoxy resin.
Machining
- Circular Power Saw
- Radial Arm Saw
- Band Saw
- Jig Saw
- Router
- Hack Saw
- Carpenters Saw
A wide range of saws can be used to cut Pultruded profiles. Factors to consider when choosing the most suitable sawing method are as follows:
(a) Cut type – straight, angled (20-80°) or curved;
(b) Pultruded Shape;
(c) Thickness;
(d) Production volume.
Diamond or carbide grit edge blades are recommended for moderate to high volume production to avoid frequent re-sharpening. Water cooled blades may be required when large cross-sectioned are being sawed.
Cutting Techniques:
- Ensure the pultrusion is adequately supported and clamped to prevent chipping.
- Clamping the pultrusion on both sides of the cut will produce a more accurate cut;
- Always apply a light even pressure when cutting;
- Avoid excessively high speeds as this will cause edges to fray;
- As a general rule, the thicker the profile, the slower the saw speed;
- Always face the surface veil side of the pultrusion upwards.
Pultruded shapes are can be drilled using standard twist drill bits or carbide drill bits if high volumes are required.
Drilling Techniques:
- Drilling speeds are equivalent to that of drilling hardwood;
- Always slowly feed drills regardless of size or speed;
- Face the surface veil side of the pultrusion upwards;
- Choose a drill bit one size larger than the hole size required, as holes drilled into pultrusions are generally 0.1mm undersized;
- Larger holes will require a back-up plate of wood to prevent `break out’ on the backside of the hole;
For large holes, a carbide or diamond coated hole saw is preferred.
Standard taps and dies can be used for threading pultruded profiles in applications where strength is not an important consideration. To improve the strength of a threaded connection an epoxy or polyester adhesive is recommended.
Straight line or angled cuts can be easily achieved on pultruded profiles with a wall thickness up to 12MM.
Routing Techniques:
- Use carbide or diamond tipped routing bits;
- Ensure only light pressure is applied when making a cut, as forcing the router bit may cause the pultrusion to heat and soften;
Pultruded profiles can be turned using a standard metal lathe and carbide tool-bits.
Turning Techniques:
- Use round-nose tool-bits and a water based coolant for a good surface finish;
- Set tool-bits slightly above the centre of your work-piece to reduce the tearing action;
- Adjust speeds to achieve the desired finish;
- Turning should be steady & continuous. The pultrusion will be noticeably marked if stopped in the middle of a pass
Grinding of Pultruded profiles is generally not recommended, as the dust created tends to quickly clog the grinding stone.
Grinding Techniques:
- Any standard grinder can be used though air-grinders are preferred;
Use coarse grit carbide grinding wheels and water as a coolant for best results; - Dress or clean grinding wheels regularly;
- Grind at high operating speeds (1500R.P.M. or above)
- For rods and tube, centreless grinding can be used to achieve
Adhesive fastening
Adhesives can provide strong and durable bonds between two FRP shapes or between FRP shapes and other structural materials. In addition to sealing joints and surfaces, adhesives distribute the stress more evenly. Satisfactory bonds will be obtained if the joint is designed to avoid excessive peeling stresses; if the mating surfaces are properly prepared and if the recommended types of adhesives are used.
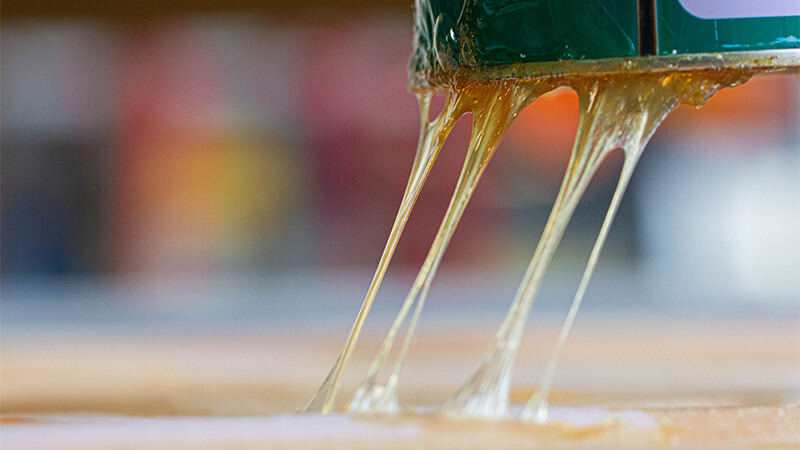